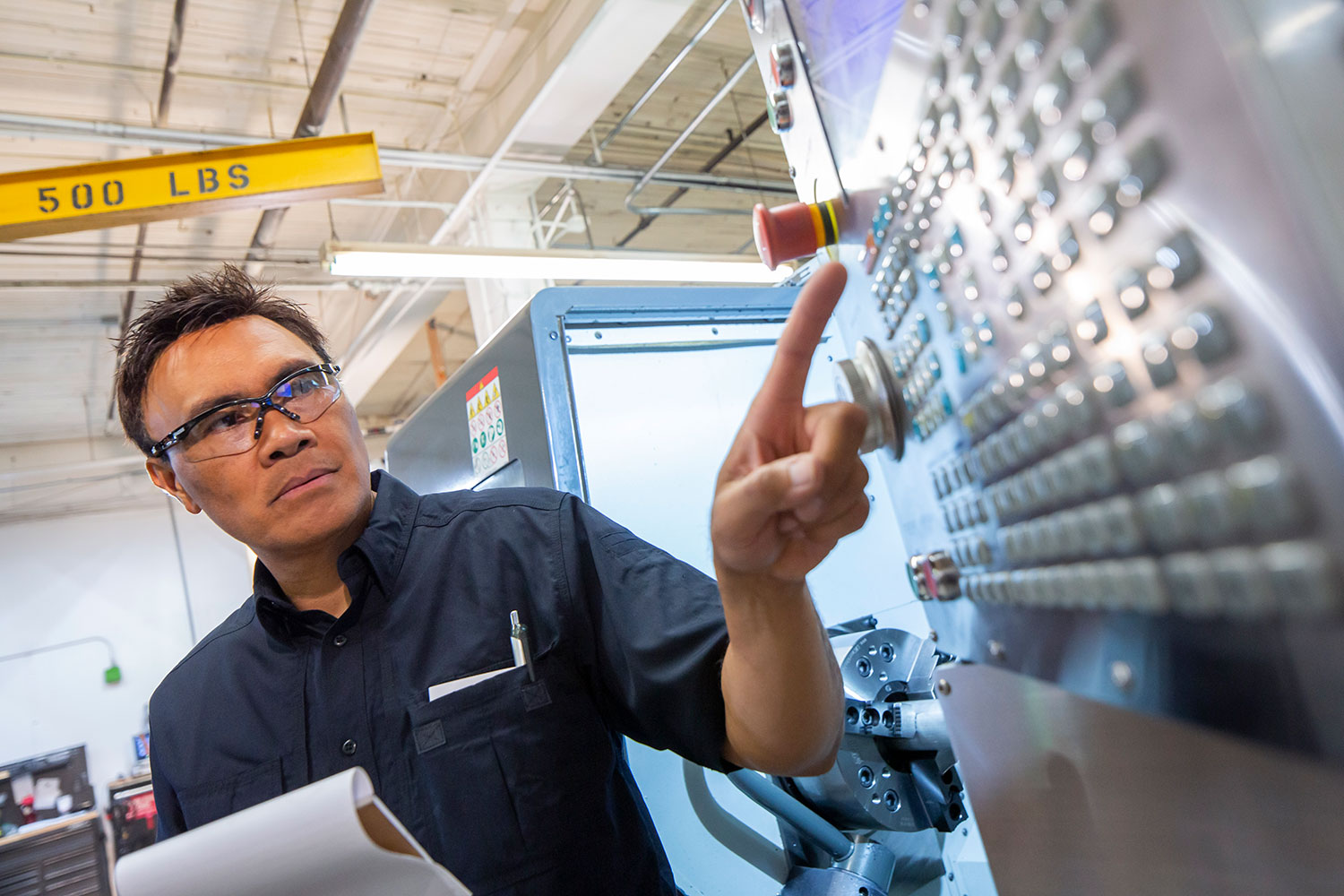
Manufacturing Plant Safety Rests on Shoulders of Management and Workers
The American economy is roaring, and manufacturing plays a vital role in that growth. After all, the sector produces the foods, cosmetics, toys, jewelry, cars and more to meet consumer demand. But ramped-up manufacturing also brings more opportunities for on-the-job injuries for the sector’s 12.7 million workers.
The U.S. Bureau of Labor Statistics (BLS) defines the manufacturing sector as “establishments engaged in the mechanical, physical, or chemical transformation of materials, substances, or components into new products.” According to its latest annual data, there were 118,050 injuries in manufacturing leading to 319 deaths in 2016. Of those injuries, 44,090 were caused by contact with objects; 42,370 occurred through overexertion and bodily reaction; 22,040 were due to falls, slips and trips; 2,590 were related to transportation incidents; and 530 stemmed from violence and other injuries by persons or animals. While these stats all marked an improvement over 2015, even one injury is one too many.
Every manufacturing facility has its own injury risks due to different equipment and processes required to make different goods, but there are some general manufacturing safety tips every facility should follow.
Create a culture of safety
Create a culture of safety by setting aggressive goals for injury-free work days and training employees to make safety a top priority. Require both new workers and tenured employees to learn manufacturing safety topics by attending mandatory classes led by a properly trained instructor. Employers should make certification classes and safety education available to all employees, and make sure the courses are updated often to account for new processes, procedures and equipment.
The workplace culture should also foster open communication between supervisors and employees, who can point out to company leadership the hazards they encounter or notice in work areas. Likewise, supervisors must create and communicate emergency action plans so workers know how to respond during emergency situations such as fire, chemical leak or personal injury. Management and employees both have a responsibility to create a safe working environment, and it’s an active and ongoing process.
Implement proper safeguards
Since the majority of manufacturing injuries stem from contact with objects and overexertion, lockout/tagout procedures, equipment safety guards, protective gear and proper lifting techniques are safety musts. There are several manufacturing safety tips employers can follow.
Lockout/tagout procedures prevent machinery and equipment from accidentally starting up and injuring workers. The Occupational Safety and Health Administration (OSHA) addresses a swath of manufacturing safety topics and offers its lockout/tagout fact sheet to help employers establish these procedures. The National Safety Council also provides a good resource for recommended lockout/tagout procedures.
Machines and equipment can expose workers to injuries such as crushed fingers or limbs, burns or blindness if the moving or sharp parts aren’t shielded properly. When used correctly, machine guards can prevent workers from contacting dangerous machine parts. Guards must be securely attached to the machine and must not create a new hazard or impede proper operation. OSHA’s complete guide to machine guarding can be found here.
Machine guards only go so far to protect workers from injury. Workers must also wear the correct personal protective equipment for the job. This includes headgear, gloves, eye protection, ear protection and foot protection. Depending on the industry, chemical, spark- or fire-resistant clothing and filtered breathing apparatuses might be necessary to protect workers. Work areas should be properly ventilated. Flammable, combustible, toxic and other hazardous materials should be stored separately and safely.
Offer on-the-job training
Many manufacturing injuries occur from slips, trips and falls. These can all be prevented by making sure aisles are clear and spills on the floor are cleaned immediately. Supervisors should walk the floor regularly and attentively to make sure there are no holes, lose tiles or boards, or foreign objects on the floor. Employees should be trained not to leave items, such as toolboxes or equipment, unattended on the floor or in areas that impede foot traffic. Work areas and emergency exits should always be clear.
Often in manufacturing, workers must use heavy equipment and move heavy items. Overexertion injuries from lifting and lowering, awkward postures or repetitive motions are common. Management should consider training workers to use the right posture when lifting. OSHA recommends workers keep their elbows close to their bodies and keep the load as close to their bodies as possible. Then, they should keep the vertical distance of lifts between mid-thigh and shoulder height. Lifting from below the waist height puts stress on legs, knees and back, while lifting above shoulder height puts stress on the upper back, shoulders and arms. OSHA also has a guide for heavy lifting and proper work posture.
While the nation’s manufacturing sector continues to grow and churn out the products consumers use every day, its owners, managers and workers share a responsibility to promote and maintain safe work environments. Following these manufacturing safety tips can help.
EMPLOYERS is committed to helping manufacturers operate safer, more efficient work places. Contact EMPLOYERS® today to learn more about our cost-effective workers’ compensation insurance.